PCB ಯಲ್ಲಿನ ಡಿಲಮಿನೇಷನ್ ಗಮನಾರ್ಹವಾದ ಕಾರ್ಯಕ್ಷಮತೆಯ ಸಮಸ್ಯೆಗಳಿಗೆ ಕಾರಣವಾಗಬಹುದು, ವಿಶೇಷವಾಗಿ ರಿಜಿಡ್-ಫ್ಲೆಕ್ಸ್ ವಿನ್ಯಾಸಗಳಲ್ಲಿ ಕಟ್ಟುನಿಟ್ಟಾದ ಮತ್ತು ಹೊಂದಿಕೊಳ್ಳುವ ಎರಡೂ ವಸ್ತುಗಳನ್ನು ಸಂಯೋಜಿಸಲಾಗಿದೆ. ಈ ಸಂಕೀರ್ಣ ಅಸೆಂಬ್ಲಿಗಳ ದೀರ್ಘಾಯುಷ್ಯ ಮತ್ತು ವಿಶ್ವಾಸಾರ್ಹತೆಯನ್ನು ಖಚಿತಪಡಿಸಿಕೊಳ್ಳಲು ಡಿಲಾಮಿನೇಷನ್ ಅನ್ನು ಹೇಗೆ ತಡೆಯುವುದು ಎಂಬುದನ್ನು ಅರ್ಥಮಾಡಿಕೊಳ್ಳುವುದು ಮುಖ್ಯವಾಗಿದೆ. ಈ ಲೇಖನವು PCB ಡಿಲಾಮಿನೇಶನ್ ಅನ್ನು ತಡೆಗಟ್ಟಲು ಪ್ರಾಯೋಗಿಕ ಸಲಹೆಗಳನ್ನು ಅನ್ವೇಷಿಸುತ್ತದೆ, PCB ಲ್ಯಾಮಿನೇಶನ್, ವಸ್ತು ಹೊಂದಾಣಿಕೆ ಮತ್ತು ಆಪ್ಟಿಮೈಸ್ಡ್ ಮ್ಯಾಚಿಂಗ್ ಪ್ಯಾರಾಮೀಟರ್ಗಳ ಮೇಲೆ ಕೇಂದ್ರೀಕರಿಸುತ್ತದೆ.
ಪಿಸಿಬಿ ಡಿಲಾಮಿನೇಷನ್ ಅನ್ನು ಅರ್ಥಮಾಡಿಕೊಳ್ಳುವುದು
ಉಷ್ಣ ಒತ್ತಡ, ತೇವಾಂಶ ಹೀರಿಕೊಳ್ಳುವಿಕೆ ಮತ್ತು ಯಾಂತ್ರಿಕ ಒತ್ತಡ ಸೇರಿದಂತೆ ವಿವಿಧ ಅಂಶಗಳಿಂದ PCB ಪದರಗಳು ಪ್ರತ್ಯೇಕವಾದಾಗ ಡಿಲಮಿನೇಷನ್ ಸಂಭವಿಸುತ್ತದೆ. ರಿಜಿಡ್-ಫ್ಲೆಕ್ಸ್ PCB ಗಳಲ್ಲಿ, ಕಠಿಣ ಮತ್ತು ಹೊಂದಿಕೊಳ್ಳುವ ವಸ್ತುಗಳ ವಿಭಿನ್ನ ಗುಣಲಕ್ಷಣಗಳಿಂದಾಗಿ ಸವಾಲು ಹೆಚ್ಚಾಗುತ್ತದೆ. ಆದ್ದರಿಂದ, ಈ ವಸ್ತುಗಳ ನಡುವಿನ ಹೊಂದಾಣಿಕೆಯನ್ನು ಖಚಿತಪಡಿಸಿಕೊಳ್ಳುವುದು ಡಿಲೀಮಿನೇಷನ್ ಅನ್ನು ತಡೆಗಟ್ಟುವಲ್ಲಿ ಮೊದಲ ಹಂತವಾಗಿದೆ.
PCB ಮೆಟೀರಿಯಲ್ ಹೊಂದಾಣಿಕೆಯನ್ನು ಖಚಿತಪಡಿಸಿಕೊಳ್ಳಿ
ಡಿಲೀಮಿನೇಷನ್ ತಡೆಗಟ್ಟುವಲ್ಲಿ ವಸ್ತುಗಳ ಆಯ್ಕೆಯು ನಿರ್ಣಾಯಕವಾಗಿದೆ. ರಿಜಿಡ್-ಫ್ಲೆಕ್ಸ್ ಪಿಸಿಬಿಯನ್ನು ವಿನ್ಯಾಸಗೊಳಿಸುವಾಗ, ಒಂದೇ ರೀತಿಯ ಉಷ್ಣ ವಿಸ್ತರಣೆ ಗುಣಾಂಕಗಳನ್ನು ಹೊಂದಿರುವ ವಸ್ತುಗಳನ್ನು ಆಯ್ಕೆ ಮಾಡುವುದು ಅತ್ಯಗತ್ಯ. ಈ ಹೊಂದಾಣಿಕೆಯು ಥರ್ಮಲ್ ಸೈಕ್ಲಿಂಗ್ ಸಮಯದಲ್ಲಿ ಒತ್ತಡವನ್ನು ಕಡಿಮೆ ಮಾಡುತ್ತದೆ, ಇದು ಡಿಲೀಮಿನೇಷನ್ಗೆ ಕಾರಣವಾಗಬಹುದು. ಹೆಚ್ಚುವರಿಯಾಗಿ, ಲ್ಯಾಮಿನೇಶನ್ ಪ್ರಕ್ರಿಯೆಯಲ್ಲಿ ಬಳಸುವ ಅಂಟಿಕೊಳ್ಳುವಿಕೆಯನ್ನು ಪರಿಗಣಿಸಿ. ರಿಜಿಡ್-ಫ್ಲೆಕ್ಸ್ ಅಪ್ಲಿಕೇಶನ್ಗಳಿಗಾಗಿ ನಿರ್ದಿಷ್ಟವಾಗಿ ವಿನ್ಯಾಸಗೊಳಿಸಲಾದ ಉತ್ತಮ-ಗುಣಮಟ್ಟದ ಅಂಟುಗಳು ಪದರಗಳ ನಡುವಿನ ಬಂಧದ ಬಲವನ್ನು ಗಮನಾರ್ಹವಾಗಿ ಹೆಚ್ಚಿಸಬಹುದು.
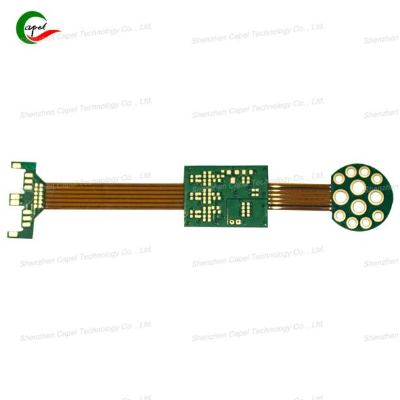
ಪಿಸಿಬಿ ಲ್ಯಾಮಿನೇಶನ್ ಪ್ರಕ್ರಿಯೆ
ಲ್ಯಾಮಿನೇಶನ್ ಪ್ರಕ್ರಿಯೆಯು PCB ತಯಾರಿಕೆಯಲ್ಲಿ ಒಂದು ಪ್ರಮುಖ ಹಂತವಾಗಿದೆ. ಸರಿಯಾದ ಲ್ಯಾಮಿನೇಶನ್ ಪದರಗಳು ಒಂದಕ್ಕೊಂದು ಚೆನ್ನಾಗಿ ಅಂಟಿಕೊಳ್ಳುತ್ತವೆ ಎಂದು ಖಚಿತಪಡಿಸುತ್ತದೆ, ಇದು ಡಿಲೀಮಿನೇಷನ್ ಅಪಾಯವನ್ನು ಕಡಿಮೆ ಮಾಡುತ್ತದೆ. ಪರಿಣಾಮಕಾರಿ PCB ಲ್ಯಾಮಿನೇಷನ್ಗಾಗಿ ಕೆಲವು ಪ್ರಾಯೋಗಿಕ ಸಲಹೆಗಳು ಇಲ್ಲಿವೆ:
ತಾಪಮಾನ ಮತ್ತು ಒತ್ತಡ ನಿಯಂತ್ರಣ: ಲ್ಯಾಮಿನೇಶನ್ ಪ್ರಕ್ರಿಯೆಯನ್ನು ಸರಿಯಾದ ತಾಪಮಾನ ಮತ್ತು ಒತ್ತಡದಲ್ಲಿ ನಡೆಸಲಾಗುತ್ತದೆ ಎಂದು ಖಚಿತಪಡಿಸಿಕೊಳ್ಳಿ. ತುಂಬಾ ಹೆಚ್ಚಿನ ತಾಪಮಾನವು ವಸ್ತುಗಳನ್ನು ಕೆಡಿಸಬಹುದು, ಆದರೆ ಸಾಕಷ್ಟು ಒತ್ತಡವು ಕಳಪೆ ಅಂಟಿಕೊಳ್ಳುವಿಕೆಗೆ ಕಾರಣವಾಗಬಹುದು.
ನಿರ್ವಾತ ಲ್ಯಾಮಿನೇಶನ್: ಲ್ಯಾಮಿನೇಶನ್ ಪ್ರಕ್ರಿಯೆಯಲ್ಲಿ ನಿರ್ವಾತವನ್ನು ಬಳಸುವುದರಿಂದ ಬಂಧದಲ್ಲಿ ದುರ್ಬಲ ಚುಕ್ಕೆಗಳನ್ನು ಉಂಟುಮಾಡುವ ಗಾಳಿಯ ಗುಳ್ಳೆಗಳನ್ನು ತೊಡೆದುಹಾಕಲು ಸಹಾಯ ಮಾಡುತ್ತದೆ. ಈ ತಂತ್ರವು PCB ಪದರಗಳಾದ್ಯಂತ ಹೆಚ್ಚು ಏಕರೂಪದ ಒತ್ತಡವನ್ನು ಖಾತ್ರಿಗೊಳಿಸುತ್ತದೆ.
ಕ್ಯೂರಿಂಗ್ ಸಮಯ: ಅಂಟಿಕೊಳ್ಳುವಿಕೆಯನ್ನು ಸರಿಯಾಗಿ ಬಂಧಿಸಲು ಸಾಕಷ್ಟು ಕ್ಯೂರಿಂಗ್ ಸಮಯವನ್ನು ಅನುಮತಿಸಿ. ಈ ಪ್ರಕ್ರಿಯೆಯನ್ನು ಹೊರದಬ್ಬುವುದು ಅಪೂರ್ಣ ಅಂಟಿಕೊಳ್ಳುವಿಕೆಗೆ ಕಾರಣವಾಗಬಹುದು, ಡಿಲೀಮಿನೇಷನ್ ಅಪಾಯವನ್ನು ಹೆಚ್ಚಿಸುತ್ತದೆ.
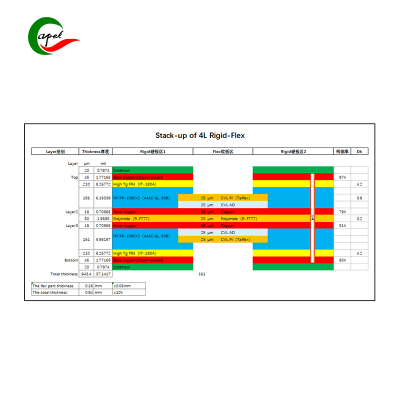
ಆಪ್ಟಿಮೈಸ್ಡ್ ರಿಜಿಡ್-ಫ್ಲೆಕ್ಸ್ ಪಿಸಿಬಿ ಮ್ಯಾಚಿಂಗ್ ಪ್ಯಾರಾಮೀಟರ್ಗಳು
ರಿಜಿಡ್-ಫ್ಲೆಕ್ಸ್ PCB ಗಳ ಸಮಗ್ರತೆಯಲ್ಲಿ ಮ್ಯಾಚಿಂಗ್ ಪ್ಯಾರಾಮೀಟರ್ಗಳು ಮಹತ್ವದ ಪಾತ್ರವನ್ನು ವಹಿಸುತ್ತವೆ. ಡಿಲಾಮಿನೇಷನ್ ಅನ್ನು ತಡೆಗಟ್ಟಲು ಕೆಲವು ಆಪ್ಟಿಮೈಸ್ ಮಾಡಿದ ಯಂತ್ರ ಸಲಹೆಗಳು ಇಲ್ಲಿವೆ:
ಕೊರೆಯುವ ತಂತ್ರಗಳು: ಕೊರೆಯುವ ಪ್ರಕ್ರಿಯೆಯಲ್ಲಿ ಶಾಖ ಉತ್ಪಾದನೆಯನ್ನು ಕಡಿಮೆ ಮಾಡಲು ಸೂಕ್ತವಾದ ಡ್ರಿಲ್ ಬಿಟ್ಗಳು ಮತ್ತು ವೇಗಗಳನ್ನು ಬಳಸಿ. ಅತಿಯಾದ ಶಾಖವು ಅಂಟಿಕೊಳ್ಳುವ ಬಂಧವನ್ನು ದುರ್ಬಲಗೊಳಿಸುತ್ತದೆ ಮತ್ತು ಡಿಲೀಮಿನೇಷನ್ಗೆ ಕಾರಣವಾಗಬಹುದು.
ರೂಟಿಂಗ್ ಮತ್ತು ಕತ್ತರಿಸುವುದು: PCB ಅನ್ನು ರೂಟಿಂಗ್ ಮಾಡುವಾಗ ಅಥವಾ ಕತ್ತರಿಸುವಾಗ, ಉಪಕರಣಗಳು ತೀಕ್ಷ್ಣವಾಗಿರುತ್ತವೆ ಮತ್ತು ಉತ್ತಮವಾಗಿ ನಿರ್ವಹಿಸಲ್ಪಡುತ್ತವೆ ಎಂದು ಖಚಿತಪಡಿಸಿಕೊಳ್ಳಿ. ಮಂದ ಉಪಕರಣಗಳು ಅತಿಯಾದ ಒತ್ತಡ ಮತ್ತು ಶಾಖವನ್ನು ಉಂಟುಮಾಡಬಹುದು, ಪದರಗಳ ಸಮಗ್ರತೆಯನ್ನು ರಾಜಿ ಮಾಡಬಹುದು.
ಎಡ್ಜ್ ಟ್ರೀಟ್ಮೆಂಟ್: ಯಂತ್ರದ ನಂತರ PCB ಯ ಅಂಚುಗಳನ್ನು ಸರಿಯಾಗಿ ಚಿಕಿತ್ಸೆ ಮಾಡಿ. ಇದು ತೇವಾಂಶದ ಒಳಹರಿವನ್ನು ತಡೆಗಟ್ಟಲು ಅಂಚುಗಳನ್ನು ಸುಗಮಗೊಳಿಸುವುದು ಅಥವಾ ಮುಚ್ಚುವಿಕೆಯನ್ನು ಒಳಗೊಂಡಿರುತ್ತದೆ, ಇದು ಕಾಲಾನಂತರದಲ್ಲಿ ಡಿಲೀಮಿನೇಷನ್ಗೆ ಕಾರಣವಾಗಬಹುದು.
PCB ಡಿಲಾಮಿನೇಷನ್ ಅನ್ನು ತಡೆಗಟ್ಟಲು ಪ್ರಾಯೋಗಿಕ ಸಲಹೆಗಳು
ಮೇಲಿನ ತಂತ್ರಗಳ ಜೊತೆಗೆ, ಕೆಳಗಿನ ಪ್ರಾಯೋಗಿಕ ಸಲಹೆಗಳನ್ನು ಪರಿಗಣಿಸಿ:
ಪರಿಸರ ನಿಯಂತ್ರಣ: ತೇವಾಂಶ ಹೀರಿಕೊಳ್ಳುವಿಕೆಯನ್ನು ತಡೆಗಟ್ಟಲು ನಿಯಂತ್ರಿತ ಪರಿಸರದಲ್ಲಿ PCB ಗಳನ್ನು ಸಂಗ್ರಹಿಸಿ. ತೇವಾಂಶವು ಅಂಟಿಕೊಳ್ಳುವ ಬಂಧವನ್ನು ದುರ್ಬಲಗೊಳಿಸುತ್ತದೆ ಮತ್ತು ಡಿಲೀಮಿನೇಷನ್ಗೆ ಕಾರಣವಾಗಬಹುದು.
ನಿಯಮಿತ ಪರೀಕ್ಷೆ: ಉತ್ಪಾದನಾ ಪ್ರಕ್ರಿಯೆಯಲ್ಲಿ ಡಿಲಾಮಿನೇಷನ್ನ ಚಿಹ್ನೆಗಳಿಗಾಗಿ PCB ಗಳ ನಿಯಮಿತ ಪರೀಕ್ಷೆಯನ್ನು ಅಳವಡಿಸಿ. ಆರಂಭಿಕ ಪತ್ತೆ ಸಮಸ್ಯೆಗಳು ಉಲ್ಬಣಗೊಳ್ಳುವ ಮೊದಲು ಅವುಗಳನ್ನು ತಗ್ಗಿಸಲು ಸಹಾಯ ಮಾಡುತ್ತದೆ.
ತರಬೇತಿ ಮತ್ತು ಜಾಗೃತಿ: PCB ಉತ್ಪಾದನಾ ಪ್ರಕ್ರಿಯೆಯಲ್ಲಿ ತೊಡಗಿರುವ ಎಲ್ಲಾ ಸಿಬ್ಬಂದಿ ಲ್ಯಾಮಿನೇಶನ್ ಮತ್ತು ಯಂತ್ರಕ್ಕೆ ಉತ್ತಮ ಅಭ್ಯಾಸಗಳಲ್ಲಿ ತರಬೇತಿ ಪಡೆದಿದ್ದಾರೆ ಎಂದು ಖಚಿತಪಡಿಸಿಕೊಳ್ಳಿ. ಡಿಲೀಮಿನೇಷನ್ಗೆ ಕಾರಣವಾಗುವ ಅಂಶಗಳ ಅರಿವು ಉತ್ತಮ ನಿರ್ಧಾರ ತೆಗೆದುಕೊಳ್ಳಲು ಕಾರಣವಾಗಬಹುದು.
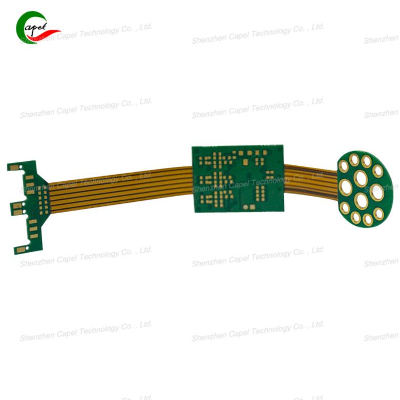
ಪೋಸ್ಟ್ ಸಮಯ: ಅಕ್ಟೋಬರ್-31-2024
ಹಿಂದೆ